ରକ୍ଷଣାବେକ୍ଷଣପ୍ୟାଲେଟ୍ ଜ୍ୟାକ୍ |କର୍ମକ୍ଷେତ୍ର ସୁରକ୍ଷା ଏବଂ ଦକ୍ଷତା ପାଇଁ ଗୁରୁତ୍ୱପୂର୍ଣ୍ଣ | ନିୟମିତ UPEEP କେବଳ ପ୍ରତିରୋଧ କରେ ନାହିଁ |ଅପ୍ରତ୍ୟାଶିତ ବ୍ରେକଡାଉନ୍ |କିନ୍ତୁ ଯନ୍ତ୍ରପାତିଗୁଡ଼ିକର ବିପଦକୁ ମଧ୍ୟ ବ olows ାନ୍ତୁ | ଚିହ୍ନଟ କରିବାପରିଧାନ କର ଏବଂ ଚିରଦିନ ପାଇଁ ଛିଣ୍ଡାଇ ଦିଅ |, ବିଶେଷକରି ଚକ ଉପରେ, ଏକ ନିରାପଦ କାର୍ଯ୍ୟ ପରିବେଶ ନିଶ୍ଚିତ କରିବା ଅତ୍ୟନ୍ତ ଜରୁରୀ | ଇଣ୍ଡଷ୍ଟ୍ରି ଶବ୍ଦ ଅନୁଯାୟୀ, ମେନ୍ରେସିଙ୍ଗକୁ ଅବହେଳା କରିବା, ଯେପରିକି ମୁଖ୍ୟ ପରିଣାମ କିମ୍ବା ସାଂଘାତିକତା ମଧ୍ୟ ହୋଇପାରେ | ତେଣୁ, ବୁ understanding ିବା |କିପରି ଠିକ୍ କରିବେ |ପ୍ୟାଲେଟ୍ ଜ୍ୟାକ୍ |ଏବଂ ଏକ ସାଧାରଣ ସମସ୍ୟା ଯାହା ସହିତ ଉତ୍ପନ୍ନ ହୁଏ |ପ୍ୟାଲେଟ୍ ଜ୍ୟାକ୍ |ଏବଂ ସେମାନଙ୍କର ସମାଧାନ ମହଙ୍ଗା ମରାମତକୁ ଏଡାଇବା ଏବଂ ଚିକ୍କଣ କାର୍ଯ୍ୟକୁ ସୁନିଶ୍ଚିତ କରିବା ପାଇଁ ପ୍ରମୁଖ |
ସାଧାରଣ ସମସ୍ୟାଗୁଡିକ ସମୀକ୍ଷା
ପ୍ୟାଲେଟ୍ ଜ୍ୟାକ୍ ଇସ୍ୟୁଗୁଡିକର ସମୀକ୍ଷା |
ନିୟମିତ ରକ୍ଷଣାବେକ୍ଷଣ ସୁରକ୍ଷା, କାର୍ଯ୍ୟଦକ୍ଷତା, ଏବଂ ଦୀର୍ଘନ୍ତ ପାଇଁ ଗୁରୁତ୍ୱପୂର୍ଣ୍ଣ |ପ୍ୟାଲେଟ୍ ଜ୍ୟାକ୍ |। ସଠିକ୍ UPKEP ଦୁର୍ଘଟଣାକୁ ପ୍ରତିରୋଧ କରିପାରିବ, ଯନ୍ତ୍ରଣାଦାୟକ ଏବଂ ମୂଲ୍ୟବାନ କ୍ଷତି | ନିୟମିତ ରକ୍ଷଣାବେକ୍ଷଣ ଯାଞ୍ଚ କରି, ବ୍ୟବସାୟଗୁଡିକ ସେମାନଙ୍କ ପ୍ୟାଲେଟ୍ ଜ୍ୟାକ୍ ର ଚିକ୍କଣ କାର୍ଯ୍ୟକୁ ନିଶ୍ଚିତ କରିପାରେ ଏବଂ ଅପ୍ରତ୍ୟାଶିତ ବ୍ରେକଡାଉନ୍ ଠାରୁ ଦୂରେଇ ରଖିପାରେ | ଏହି ସକ୍ରିୟ ଉପାୟ କେବଳ ୱାର୍କପ୍ଲେସ ନିରାପତ୍ତା କୁ ବ ens ାଇଥାଏ କିନ୍ତୁ ଅପରେସନ୍ସର ସାମଗ୍ରିକ ଦକ୍ଷତା ସହିତ ମଧ୍ୟ ଯୋଗଦାନ କରେ |
ଯେତେବେଳେ ଏହା ଆସେ |ପ୍ୟାଲେଟ୍ ଜ୍ୟାକ୍ |ସମସ୍ୟା, ପ୍ରାରମ୍ଭିକ ପରିଚୟ ହେଉଛି ଚାବି | ସେମାନଙ୍କର ପ୍ରାରମ୍ଭିକ ପର୍ଯଜ୍ଠରେ ସାଧାରଣ ସମସ୍ୟା ଚିହ୍ନିବା ଦ୍ୱାରା ଅପରେଟର୍ମାନେ ଅଧିକ ଗୁରୁତ୍ୱପୂର୍ଣ୍ଣ ପ୍ରସଙ୍ଗରେ ବୃଦ୍ଧି କରିବା ପୂର୍ବରୁ ଅପରେଟର୍ମାନଙ୍କୁ ତୁରନ୍ତ ସମାଧାନ କରିପାରିବେ | ଉଦାହରଣ ସ୍ୱରୂପ, ଚିହ୍ନର ଲକ୍ଷ୍ୟ |ପିନ୍ଧ ଆଉ ଚିରଚକଗୁଡିକ ଉପରେ କିମ୍ବାହାଇଡ୍ରାହୀନ ସିଷ୍ଟମ୍ |ତୁରନ୍ତ ଧ୍ୟାନ ପାଇଁ ଏକ ଆବଶ୍ୟକତା ସୂଚାଇପାରେ | ସମୟାନୁକ୍ରମିକ ହସ୍ତକ୍ଷେପ ପାଇଁ ଏହି ସମସ୍ୟାର ସମାଧାନ ଏବଂ କାର୍ଯ୍ୟ ପ୍ରବାହରେ ସମ୍ଭାବ୍ୟ ବ୍ୟାଘାତକୁ ରୋକିଥାଏ |
ଏକ ପ୍ୟାଲେଟ୍ ଜ୍ୟାକ୍ କିପରି ଠିକ୍ କରିବେ |
ଠିକଣାପ୍ୟାଲେଟ୍ ଜ୍ୟାକ୍ |ସାଧାରଣ ତ୍ରୁଟି ନିବାରଣ ପଦକ୍ଷେପଗୁଡ଼ିକୁ ପ୍ରଭାବଶାଳୀ ଭାବରେ ଆବଶ୍ୟକ କରେ | ଏହି ପଦକ୍ଷେପଗୁଡ଼ିକ ବ୍ୟବସ୍ଥିତକୁ ନିରାକରଣ କରିସାକୁ ସମସ୍ୟାକୁ ଯୋଗାଇ ଦେଇଥାଏ, ଏବଂ ଉପଯୁକ୍ତ ସମାଧାନକୁ କାର୍ଯ୍ୟକାରୀ କରିବା | ଏକ ସଂରଚନା ପଦ୍ଧତିରେ ସମସ୍ୟା ସମାଧାନକୁ ନିକଟତର କରି, ଅପରେଟର୍ ଗୁଡିକ ନିଶ୍ଚିତ ଭାବରେ ସମସ୍ୟା ସମାଧାନ କରିପାରିବେ ଏବଂ ସେମାନଙ୍କ ଉପକରଣର କାର୍ଯ୍ୟକାରିତା ପୁନ restore ସ୍ଥାପନ କରିପାରିବେ |
ଠିକ-ଫିକ୍ସିଂର ଉପଯୁକ୍ତ ନିରାକରଣ ହେଉଛି ଏକ ଜଟିଳ ଦିଗ |ପ୍ୟାଲେଟ୍ ଜ୍ୟାକ୍ |ସମସ୍ୟାଗୁଡିକ କ red ଣସି ମରାମତି କିମ୍ବା ସଂଶୋଧନ କରିବାକୁ, ଏହି ସମସ୍ୟାର ଉତ୍ସକୁ ସଠିକ୍ ଭାବରେ ସୂଚିତ କରିବା ଜରୁରୀ | ଏହା ବିଭିନ୍ନ ଉପାଦାନଗୁଡ଼ିକୁ ଯାଞ୍ଚ କରିପାରେ ଯେପରିକି ହାଇଡ୍ରୋଲିକ୍ ସିଷ୍ଟମ, ଫଙ୍କ୍ସ, କିମ୍ବାତେଲ ଲଗାନ୍ତୁ |ଯେକ any ଣସି ଅନାବଶ୍ୟକ ଚିହ୍ନଟ କରିବାକୁ ପଏଣ୍ଟ | ପୁଙ୍ଖାନୁହି ରୋଗ ମାଧ୍ୟମରେ, ଅପରେଟର୍ସଗୁଡିକ ଏହା କେବଳ ଏହାର ଲକ୍ଷଣ ଅପେକ୍ଷା ଅନ୍ତର୍ନିହିତ ସମସ୍ୟାର ସମାଧାନ କରୁଛନ୍ତି |
ତେଲଯୁକ୍ତ ସମସ୍ୟା |
ଲବ୍ରିକେସନ୍ ମାଧ୍ୟମରେ ସୁଗମ କାର୍ଯ୍ୟରେ ସୁଗମ କାର୍ଯ୍ୟଗୁଡିକ ଗତିଶୀଳ ଅଂଶଗୁଡିକ ଗତିଶୀଳ ଅଂଶଗୁଡିକ ଦୂର କରିଥାଏ, ଆପଣଙ୍କ ଉପକରଣର ଜୀବନଶଜୀବୀକୁ ବିସ୍ତାର କରିଥାଏ | ସଠିକ୍ ତେଲ ଆପଣଙ୍କ କାର୍ଯ୍ୟକାରିତା ବଜାୟ ରଖିବାରେ ଏକ ଗୁରୁତ୍ୱପୂର୍ଣ୍ଣ ଭୂମିକା ଗ୍ରହଣ କରେ |ପ୍ୟାଲେଟ୍ ଜ୍ୟାକ୍ |। ଫୁଙ୍ଗା ଏବଂ ଗଣ୍ଠି ପରି ଘୁରିଷ୍ଠାଗଣ ଏବଂ ଗଣ୍ଠି ସୁଗମ କାର୍ଯ୍ୟରେ ପୋଷାକ ଏବଂ ଲୁହକୁ ହ୍ରାସ କରେ |
ଗରିବ ତେଲଯୁକ୍ତ |
ଗରିବ ତେଲର କାରଣ |
- ନିୟମିତ ରକ୍ଷଣାବେକ୍ଷଣ କାର୍ଯ୍ୟସୂଚୀ ଅବହେଳା କରୁଛି |
- ଭୁଲ କିମ୍ବା ନିମ୍ନ ମାନର ଲବ୍ରିକାଣ୍ଟ ବ୍ୟବହାର କରି |
- ଧୂଳି ଏବଂ ଆବର୍ଜନା ସଂଗ୍ରହକୁ ସଠିକ୍ ତେଲ କରିବା ପାଇଁ ପରିବେଶ କାରକ |
ତେଲ ଲଗାଇବା ପାଇଁ ସମାଧାନ |
- ଲବ୍ରିକେସନ୍ ଫ୍ରିକ୍ୱେନ୍ସି ପାଇଁ ଉତ୍ପାଦକ ନିର୍ଦ୍ଦେଶାବଳୀ ଅନୁସରଣ କରନ୍ତୁ |
- ଉଚ୍ଚ-ଗୁଣବତ୍ତା ବ୍ୟବହାର କରନ୍ତୁ, ସୁପାରିଶ କରାଯାଇଥିବା ଲବ୍ରିକାଣ୍ଟଗୁଡିକ ଉପଯୁକ୍ତ |ପ୍ୟାଲେଟ୍ ଜ୍ୟାକ୍ |.
- ପ୍ରଭାବଶାଳୀତା ନିଶ୍ଚିତ କରିବାକୁ ଲବ୍ରିକାଣ୍ଟ ଲଗାଇବା ପୂର୍ବରୁ ନିୟମିତ ଭାବରେ ଧର୍ମ ଖାଇବା ଅଂଶଗୁଡ଼ିକୁ ସଫା କରିବା |
ପ୍ରତିଷେଧକ ପଦକ୍ଷେପ |
ନିୟମିତ ତେଲଯୁକ୍ତ କାର୍ଯ୍ୟସୂଚୀ |
- ସମୟସୀମା ଲବ୍ରିକେସନ୍ ବ୍ୟବଧାନ ପାଇଁ ଏକ ରକ୍ଷଣାବେକ୍ଷଣ କ୍ୟାଲେଣ୍ଡର ସୃଷ୍ଟି କରନ୍ତୁ |
- ଅନୁପଯୁକ୍ତ ତେଲ ନିଷ୍କାସନର କ signs ଣସି ଚିହ୍ନ ଚିହ୍ନଟ କରିବାକୁ ନିୟମିତ ଭାବରେ ଗତିଶୀଳ ଅଂଶକୁ ଯାଞ୍ଚ କରନ୍ତୁ |
ସୁପାରିଶ କରାଯାଇଥିବା ଲବ୍ରିକାଣ୍ଟ |
- ସର୍ବୋତ୍କୃଷ୍ଟ କାର୍ଯ୍ୟଦକ୍ଷତା ପାଇଁ ଲିଥିୟମ୍-ଆଧାରିତ ଗ୍ରେଜ୍ ବ୍ୟବହାର କରନ୍ତୁ |
- ବଣ୍ଟିତ ସ୍ଥାୟୀତା ଏବଂ ଅତ୍ୟାଧୁନିକତା ପାଇଁ ସିନ୍ଥେଟିକ୍ ତେଲକୁ ବିଚାର କରନ୍ତୁ |
ତୁମକୁ ତେଲ ଲଗାଇବାପ୍ୟାଲେଟ୍ ଜ୍ୟାକ୍ |ଗତିଶୀଳ ଅଂଶଗୁଡ଼ିକ ହେଉଛି ଏକ ଗୁରୁତ୍ୱପୂର୍ଣ୍ଣ କାର୍ଯ୍ୟ ଯାହାକି କିଛି ପ୍ରସ୍ତୁତି ଏବଂ ସତର୍କତା ଆବଶ୍ୟକ କରେ | ପ୍ରଥମେ, ମେଳା, ଧୂଳି, କିମ୍ବା ଆବର୍ଜନା ବାହାର କରିବା ପାଇଁ କପଡା ଅଂଶଗୁଡ଼ିକୁ ଏକ କପଡା କିମ୍ବା ବ୍ରଶ୍ ସଫା କରନ୍ତୁ | ତା'ପରେ, ଏକ ଉପଯୁକ୍ତ ଉପକରଣ ବ୍ୟବହାର କରନ୍ତୁ ଯେପରିକି ଏକ ଗ୍ରୀସ୍ ବନ୍ଧୁକ କିମ୍ବା ଧାଂସମୟ ଅଂଶକୁ ଗତିଶୀଳ ଅଂଶରେ ପ୍ରୟୋଗ କରିବା ପାଇଁ | ଚକ, ବିୟରିଂ, ଆକ୍ସେସ୍, ଶୃଙ୍ଖଳା, ଫଙ୍କସ୍, ଏବଂ ହାଇଡ୍ରୋଲିକ୍ ପମ୍ପ ଭଳି ଅତ୍ୟଧିକ ଉନ୍ମୋଚିତ ଅଂଶ ଉପରେ ଧ୍ୟାନ ଦିଅନ୍ତୁ |
ପରେ, ଏକ କପଡା କିମ୍ବା କାଗଜ ଟାୱେଲ ସହିତ କ exp ଣସି ଅତିରିକ୍ତ ଲବ୍ରିକାଣ୍ଟକୁ ପୋଛି ଦିଅ | ଶେଷରେ, ତୁମର ପରୀକ୍ଷା କର |ପ୍ୟାଲେଟ୍ ଜ୍ୟାକ୍ |ଚପିତ, ଜାମିଙ୍ଗ୍, କିମ୍ବା ଲିକ୍ ପରି କ ast ଣସି ଅସ୍ୱାଭାବିକତା ଯାଞ୍ଚ କରନ୍ତୁ | ଏହି ସର୍ବୋତ୍ତମ ଅଭ୍ୟାସ ଅନୁସରଣ କରି ଆପଣ ନିଶ୍ଚିତ କରିପାରିବେ ଯେ ଆପଣଙ୍କର |ପ୍ୟାଲେଟ୍ ଜ୍ୟାକ୍ |ଭଲ-ତେଲିଆ ଏବଂ ଚୁଲିରେ କାର୍ଯ୍ୟ କରୁଛି |
ଉତ୍ପାଦକଙ୍କ ନିର୍ଦ୍ଦେଶ ଅନୁଯାୟୀ ନିୟମିତ ଗତି କରୁଥିବା ଅଂଶଗୁଡ଼ିକୁ ନିୟମିତ ଲବ୍ରିକ କରନ୍ତୁ; ଏହା ଘର୍ଷଣର ଜୀବନଶ server ଚାଳୟକୁ ଯଥେଷ୍ଟ ବିସ୍ତାର କରିବାବେଳେ ଘର୍ଷଣ ଏବଂ ପିନ୍ଧିବାରେ ସାହାଯ୍ୟ କରେ |
ହାଇଡ୍ରୋଲିକ୍ ସିଷ୍ଟମ୍ ସମସ୍ୟା |
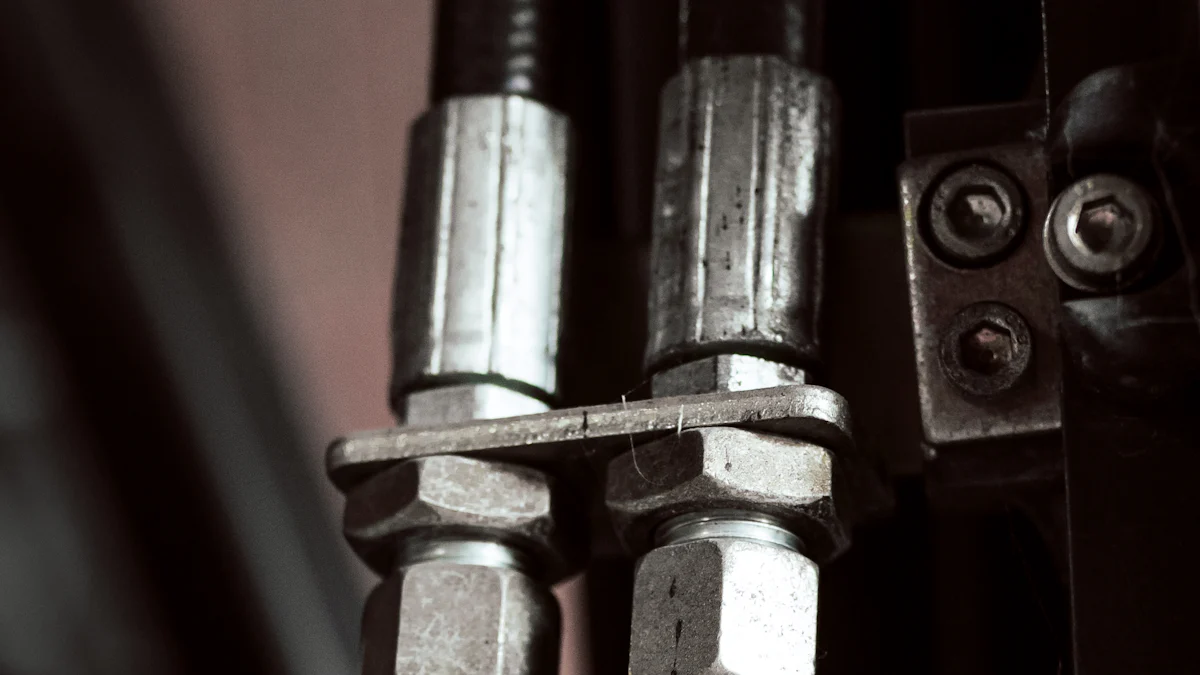
ହାଇଡ୍ରୋଲିକ୍ ସିଷ୍ଟମରେ ଫାଟିଯାଇଥିବା ବାୟୁ |
ପ୍ରଦର୍ଶିତ ରିସେପୁଥିବା ଯନ୍ତ୍ରପାତି ନିରାକରଣ ସହିତ ସମସ୍ୟାଗୁଡ଼ିକୁ ନିର୍ଣ୍ଣୟ କରିବା ପାଇଁ ସମସ୍ୟାଗୁଡିକ ନିର୍ଣ୍ଣୟ କରିବା ପାଇଁ ଇକ୍ଷଳ୍ପ ଚାରଣତା ଏବଂ କାର୍ଯ୍ୟକାରୀ କରିବା ପାଇଁ ନିର୍ଗତ ଯନ୍ତ୍ରଗୁଡ଼ିକ ନିର୍ଣ୍ଣୟ କରିବା ପାଇଁ ଜରୁରୀ | ସାଧାରଣଇପୋର୍ଟିଂ ପଦକ୍ଷେପ ଗୁଡିକରେ ହାଇଡ୍ରାଞ୍ଚିକ୍ ଫ୍ଲୁଇଡ୍ ସ୍ତର ଅନ୍ତର୍ଭୂକ୍ତ କରେ |ନିୟନ୍ତ୍ରଣ ଭାରକୁ ଯାଞ୍ଚ କରି ପମ୍ପ୍ନତି ସହିତ କାର୍ଯ୍ୟ କରିବା ପାଇଁ ପମ୍ପନିୟଲି ପରୀକ୍ଷା କରିବା |
- ଫସି ରହିଥିବା ପବନର କାରଣ:
- ନିୟମିତ ରକ୍ଷଣାବେକ୍ଷଣ କାର୍ଯ୍ୟସୂଚୀ ଅବହେଳା କରିବା ହାଇଡ୍ରୋଲିକ୍ ସିଷ୍ଟମରେ ଫସିଯିବା ଘରକୁ ନେଇପାରେ |
- ରକ୍ଷଣାବେକ୍ଷଣ କିମ୍ବା ମରାମତି ପରେ ସିଷ୍ଟମର ଅନୁପଯୁକ୍ତ ରକ୍ତସ୍ରାବ ହେଉଛି ଏୟାର ପକେଟ୍ ହୋଇପାରେ |
- କ୍ଷତିଗ୍ରସ୍ତ ସିଲ୍ କିମ୍ବା ସଂଯୋଗଗୁଡ଼ିକ ହାଇଡ୍ରୋଲିକ୍ ସିଷ୍ଟମରେ ପ୍ରବେଶ କରିବାକୁ ବାୟୁକୁ ଅନୁମତି ଦେଇପାରେ |
- ଫସି ରହିଥିବା ବାୟୁ ପାଇଁ ସମାଧାନ:
- ଉତ୍ପାଦନକର ନିର୍ଦ୍ଦେଶାବଳୀ ଅନୁସରଣ କରି ଉଚ୍ଚତୟିକାରୀ ସିଷ୍ଟମକୁ ପୂର୍ଣ୍ଣ ଭାବରେ ପ୍ରଜ୍ୱଳିତ କରି ଶବ୍ଦ କଲେ |
- ସିଷ୍ଟମରୁ ବ୍ୟାପକ ବାୟୁକୁ ପ୍ରଭାବଶାଳୀ ଭାବରେ ହଟାଇବା ପାଇଁ ଏକ ଉପଯୁକ୍ତ ରକ୍ତସ୍ରାବ ଉପକରଣ ବ୍ୟବହାର କରନ୍ତୁ |
- ସମସ୍ତ ସିଲ୍ ଏବଂ କ୍ଷତିର କ signsions ଣସି ଲକ୍ଷଣ ପାଇଁ ଯାଞ୍ଚ ଯାଞ୍ଚ କରନ୍ତୁ ଏବଂ ଯଦି ଆବଶ୍ୟକ ହୁଏ ତେବେ ସେମାନଙ୍କୁ ବଦଳାନ୍ତୁ |
କ୍ଷତିଗ୍ରସ୍ତଓ-ରିଙ୍ଗଗୁଡିକ
ଜ୍ୟାକର ଲିଫ୍ଟ ଏବଂ ନିମ୍ନ କାର୍ଯ୍ୟ କାର୍ଯ୍ୟ ପାଇଁ ହାଇଡ୍ରୋଲିକ୍ ସିଷ୍ଟମ୍ ଦାୟୀ |ଯେକ any ଣସି ଲିକ୍ ଯାଞ୍ଚ କରନ୍ତୁ |କିମ୍ବା କ୍ଷତି ଯଦି ଆପଣ କ (ଣସି ସମସ୍ୟାକୁ ଲକ୍ଷ୍ୟ କରନ୍ତି, ତେବେ ସେମାନଙ୍କୁ ତୁରନ୍ତ ମରାମତି କରନ୍ତୁ |
- ନଷ୍ଟ ହୋଇଥିବା ଓ-ରିଙ୍ଗର କାରଣ:
- ସଠିକ୍ ରକ୍ଷଣାବେକ୍ଷଣ ବିନା କ୍ରମାଗତ ବ୍ୟବହାର ପୋଷାକ ଓ-ରିଙ୍ଗରେ ପିନ୍ଧିବା ଏବଂ ଲୁହ ହୋଇପାରେ |
- ଅତ୍ୟଧିକ ତାପମାତ୍ରା କିମ୍ବା ରାସାୟନିକ ପଦାର୍ଥ ପରି କଠୋର ପରିବେଶ ପରିସ୍ଥିତିର ଏକ୍ସପୋଜର ଓ-ରିଙ୍ଗକୁ ଖରାପ କରିପାରେ |
- ଉପାଦାନଗୁଡ଼ିକର ଭୁଲ ସ୍ଥାପନ କିମ୍ବା ଅତ୍ୟଧିକ ଟାଣିବା ସମୟ ସହିତ ଓ-ରିଙ୍ଗକୁ ନଷ୍ଟ କରିପାରେ |
- କ୍ଷତିଗ୍ରସ୍ତ O- ରିଙ୍ଗ ପାଇଁ ସମାଧାନ:
- କ୍ଷତିଗ୍ରସ୍ତ ଓ-ରିଙ୍ଗରେ କ red ଣସି ମରାମତି ପାଇଁ ହାଇଡ୍ରୋଲିକ୍ ସିଷ୍ଟମକୁ ପାୱାର୍ କଟିଦିଅ |
- ଅଧିକ କ୍ଷତି ନକରି ଉପଯୁକ୍ତ ଉପକରଣ ବ୍ୟବହାର କରି କ୍ଷତିଗ୍ରସ୍ତ ଓ-ରିଙ୍ଗକୁ ଯତ୍ନର ସହିତ ଅପସାରଣ କରନ୍ତୁ |
- ସଠିକ୍ ଆକାର ଏବଂ ସାମଗ୍ରୀର ଏକ ନୂତନ ଓ-ରିଙ୍ଗ ଇନଷ୍ଟଲ୍ କରନ୍ତୁ, ଭବିଷ୍ୟତର ସମସ୍ୟାଗୁଡିକ ରୋକିବା ପାଇଁ ଏକ ଉପଯୁକ୍ତ ସିଲ୍ ସୁନିଶ୍ଚିତ କରିବା |
ହାଇଡ୍ରୋଲିକ୍ ୟୁନିଟ୍ କୁ ନିୟମିତ ଭାବେ ସମ୍ଭାବ୍ୟ ସମସ୍ୟାର ଶୀଘ୍ର ଚିହ୍ନଟ କରିବା ଅତ୍ୟନ୍ତ ଗୁରୁତ୍ୱପୂର୍ଣ୍ଣ | ଫାଟେଡ୍ ବାୟୁ ଏବଂ ନଷ୍ଟ ହୋଇଥିବା ଓ-ରିଙ୍ଗଗୁଡିକ ଠିକଣା କରି ତୁରନ୍ତ, ଅପରେଟର୍ସ ସେମାନଙ୍କର ପ୍ୟାଲେଟ୍ ଜାତିର ସର୍ବୋତାମୂଳକ କାର୍ଯ୍ୟଦକ୍ଷତା ପ୍ରଦର୍ଶନ କରିପାରିବେ ଏବଂ ଉତ୍ସାହରୁ ଅଧିକ ଗୁରୁତ୍ୱପୂର୍ଣ୍ଣ ସମସ୍ୟାଗୁଡିକ ରୋକନ୍ତୁ | ମନେରଖନ୍ତୁ ଯେ ସଠିକ୍ ରକ୍ଷଣାବେକ୍ଷଣ କେବଳ ନିରାପତ୍ତାକୁ ସୁନିଶ୍ଚିତ କରେ ନାହିଁ କିନ୍ତୁ ଏକ ଆନୁଷ୍ଠାନିକ ଜୀବନଶ wifferent ାଧୀନ କାର୍ଯ୍ୟକ୍ଷେତ୍ରରେ ଯୋଗଦାନ କରେ |
ଭୁଲ୍ ଭୁଲ ତଥ୍ୟ |
କେବେପ୍ୟାଲେଟ୍ ଜ୍ୟାକ୍ |ପ୍ରଦର୍ଶନୀ ଭୁଲ ଭୁଲ ଭାବରେ ପ୍ରଦର୍ଶନ କରନ୍ତୁ, ଏହା ସେମାନଙ୍କର କାର୍ଯ୍ୟକ୍ଷମ ଦକ୍ଷତାକୁ ଯଥେଷ୍ଟ ପ୍ରଭାବ ପକାଇପାରେ |କ୍ରମାଗତ ବ୍ୟବହାର ସମସ୍ୟା |ଏହି ସମସ୍ୟାର ଏକ ସାଧାରଣ କାରଣ, ଅସମାନ ଫଙ୍କଗୁଡିକୁ ଅଗ୍ରଣୀ ଯାହା ଏହାକୁ ଫଳପ୍ରଦ ଭାବରେ ମନିଭର୍ ପାଇଁ ଚ୍ୟାଲେଞ୍ଜ କରିଥାଏ | ଭୁଲ ତଥ୍ୟ କେବଳ ଭାରର ସ୍ଥିରତାକୁ ପ୍ରଭାବିତ କରେ ନାହିଁ କିନ୍ତୁ କର୍ମକ୍ଷେତ୍ରରେ ସୁରକ୍ଷା ବିପଦ ମଧ୍ୟ ପକାଇଥାଏ | ଉପଭୋକ୍ତାମାନେ ପାଲଲେଟ୍ ତଳେ ଥିବା କାର୍ଯ୍ୟକୁ ସଠିକ୍ ଭାବରେ ରଖିବା ପାଇଁ ସଂଘର୍ଷ କରିପାରନ୍ତି, ଫଳସ୍ୱରୂପ ସମ୍ଭାବ୍ୟ ଦୁର୍ଘଟଣା କିମ୍ବା ଦ୍ରବ୍ୟର କ୍ଷତି |
ପାଠ କରିବାକୁଭୁଲ୍ ଭୁଲ ତଥ୍ୟ |, ଅପରେଟରମାନେ ବିଚାର କରିପାରିବେ |ଫର୍କିଂ ଫଙ୍କସ୍ |ଏକ ବ୍ୟବହାରିକ ସମାଧାନ ଭାବରେ | ସେମାନେ ସ୍ତରୀୟ ଏବଂ ସମାନ୍ତରାଳ ବୋଲି ନିଶ୍ଚିତ କରିବାକୁ କ rucks ଶଳକୁ ସଜାଡିବା ଦ୍ୱାରା, ଉପଭୋକ୍ତାମାନେ କାର୍ଯ୍ୟକାରିତାକୁ ଉନ୍ନତ କରିପାରିବେ |ପ୍ୟାଲେଟ୍ ଜ୍ୟାକ୍ |ଏବଂ ଲୋଡ୍ ଭାରିଙ୍ଗ୍ କ୍ଷମତା ବ ens ାନ୍ତୁ | ଉପଯୁକ୍ତ ଆଲାଇନ୍ମେଣ୍ଟ କେବଳ ସୁଗନ୍ଧିତ ପ୍ୟାଲେଟ୍ ସନ୍ନିବେଶ ଏବଂ ନିଷ୍କାସନକୁ ସହଜ କରିଥାଏ ଏବଂ ଅସମ୍ଭବ ଭାର ସହିତ ଜଡିତ ଦୁର୍ଘଟଣାର ବିପଦକୁ ମଧ୍ୟ କମ୍ କରିଥାଏ |
ଭୁଲ୍ ଭୁଲ ତଥ୍ୟ ପାଇଁ ସମାଧାନ |
ଫର୍କିଂ ଫଙ୍କସ୍ |
- ଇଙ୍କି ଆଲାଇନ୍ମେଣ୍ଟ ଯାଞ୍ଚ କରନ୍ତୁ:କ any ଣସି ଅସଙ୍ଗତିକୁ ଚିହ୍ନିବା ପାଇଁ ଫଙ୍କଗୁଡିକର ସାମ୍ପ୍ରତିକ ଆଲାଇନ୍ମେଣ୍ଟକୁ ପରୀକ୍ଷା କରି ଆରମ୍ଭ କରନ୍ତୁ |
- ଫଙ୍କ୍ ପୋଜିସନ୍ ଆଡଜଷ୍ଟ କରନ୍ତୁ:ଉପଯୁକ୍ତ ସାଧନ ବ୍ୟବହାର କରି, ସେମାନେ ସମାନ୍ତରାଳ ଏବଂ ସମାନ ଉଚ୍ଚତାରେ ଥିବା ସମାନ ଉଚ୍ଚତାରେ ଥିବାବେଳେ କ relows ଶଳକୁ ଯତ୍ନର ସହିତ ରାଗିଛନ୍ତି |
- ପରୀକ୍ଷା କାର୍ଯ୍ୟକାରିତା:ରାଇଟମେଣ୍ଟ ପରେ, ପରୀକ୍ଷା କରନ୍ତୁ |ପ୍ୟାଲେଟ୍ ଜ୍ୟାକ୍ |ଏହାକୁ ଏକ ଷ୍ଟାଣ୍ଡାର୍ଡ ପ୍ୟାଲେଟରେ ରଖିବା ପାଇଁ ଏହାକୁ ଏକ ଷ୍ଟାଣ୍ଡାର୍ଡ ପ୍ୟାଲେଟ୍ ତଳେ ଭର୍ତ୍ତି କରି ଯାଞ୍ଚ କରି ସେହି ଉଭୟ ଫିକ୍ସକୁ ସୁଗମ କରେ |
- ସୂକ୍ଷ୍ମ-ଟ୍ୟୁନ୍ ଆଲାଇନ୍ମେଣ୍ଟ୍:ଯଦି ଦକ୍ଷ ପାଲଲେଟ୍ ନିୟନ୍ତ୍ରଣ ପାଇଁ ସର୍ବୋଚ୍ଚ ଆଲାଇନ୍ମେଣ୍ଟ ହାସଲ କରିବାକୁ ଆବଶ୍ୟକ ହୁଏ ତେବେ ଛୋଟ ଆଡଜଷ୍ଟମେଣ୍ଟ୍ କରନ୍ତୁ |
ପ୍ରତିଷେଧକ ପଦକ୍ଷେପ |
- ନିୟମିତ ଯାଞ୍ଚ:ମିସାଲାଇନ୍ ର କ signs ଣସି ଚିହ୍ନର କ signs ଣସି ଚିହ୍ନକୁ ଚିହ୍ନଟ କରିବା ପାଇଁ କାଉଣ୍ଟର ଯାଞ୍ଚ କରନ୍ତୁ |
- ଅପରେଟର୍ ଟ୍ରେନିଂ:ସଠିକ୍ ହ୍ୟାଣ୍ଡଲିଂ କ ques ଶଳ ଉପରେ ଅପରେଟରମାନଙ୍କୁ ତାଲିମ ପ୍ରଦାନ କରନ୍ତୁ ଏବଂ ଫଙ୍କ୍ ମିସାଲାଇନର ଲକ୍ଷଣଗୁଡିକ କିପରି ଚିହ୍ନଟ କରିବେ |
- ରକ୍ଷଣାବେକ୍ଷଣ ରେକର୍ଡ:ରକ୍ଷଣାବେକ୍ଷଣ ପ୍ରକ୍ରିୟାକରଣ ପ୍ରକ୍ରିୟା ଏବଂ ତାରିଖ ସହିତ ରକ୍ଷଣାବେକ୍ଷଣ କାର୍ଯ୍ୟକଳାପର ବିସ୍ତୃତ ରେକର୍ଡଗୁଡିକ ରଖନ୍ତୁ |
ଏହି ସମାଧାନ ଏବଂ ପ୍ରତିଷେଧକ ବ୍ୟବସ୍ଥାକୁ କାର୍ଯ୍ୟକାରୀ କରି, ବ୍ୟବସାୟଗୁଡିକ ସେମାନଙ୍କ ମଧ୍ୟରେ ଫଙ୍କ୍ ଭୁଲ୍ ସହିତ ଜଡିତ ବିପଦକୁ ହ୍ରାସ କରିପାରେ |ପ୍ୟାଲେଟ୍ ଜ୍ୟାକ୍ |। ଏହି ଫିକ୍ସ ନିଶ୍ଚିତ ଭାବରେ ସଠିକ୍ ଭାବରେ ପରିଚାଳିତ ହେଉଛି କେବଳ କାର୍ଯ୍ୟକ୍ଷମ ସୁରକ୍ଷା ଉପରେ ବ ens େ କିନ୍ତୁ ଡୋ wewntime ହ୍ରାସ କରି downtime ହ୍ରାସ କରି downingime ହ୍ରାସ କରି ସାମଗ୍ରିକ ଉତ୍ପାଦନରେ ଅବଦାନ ପ୍ରଦାନ କରି |
ତେଲ ପମ୍ପସମସ୍ୟାଗୁଡିକ
ସାଧାରଣ ତେଲ ପମ୍ପ ସମସ୍ୟା |
ତେଲ ପମ୍ପ ଇସ୍ୟୁଗୁଡ଼ିକର କାରଣ |
- ନିୟମିତ ତେଲ ପମ୍ପ ରକ୍ଷଣାବେକ୍ଷଣକୁ ଅବହେଳା କରିବା ସମୟ ସହିତ ପମ୍ପ ଦକ୍ଷତା ଏବଂ କାର୍ଯ୍ୟଦକ୍ଷତା ମଧ୍ୟରେ ହ୍ରାସ ଘଟାଇପାରେ |
- ଭୁଲ ପ୍ରକାରର ହାଇଡ୍ରୋଲିକ୍ ତେଲ ବ୍ୟବହାର କରି କିମ୍ବା ତେଲ ସ୍ତର ଯାଞ୍ଚ କରିବାରେ ବିଫଳ ହୁଏ |ଅନୁପଯୁକ୍ତ ତେଲ |ଏବଂ ପମ୍ପ ତ୍ରୁଟି ସୃଷ୍ଟି କରେ |
- ଧୂଳି ପରି ପରିବେଶ କାରକ, ଡରିସ୍, କିମ୍ବା ଆର୍ଦ୍ରତା ପ୍ରଦୂଷଣ ହାଇଡ୍ରୋଲିକ୍ ଫ୍ଲୁଇଡର ଗୁଣକୁ ପ୍ରଭାବିତ କରି ତେଲ ପମ୍ପ ସମସ୍ୟାରେ ଯୋଗଦାନ କରିପାରିବ |
ତେଲ ପମ୍ପ ସମସ୍ୟା ପାଇଁ ସମାଧାନ |
- ନିୟମିତ ତେଲ ପମ୍ପ ରକ୍ଷଣାବେକ୍ଷଣ |:
- କାର୍ଯ୍ୟକାରୀ ପାଠ୍ୟକ୍ରମ ଲିକ୍, ପରୀକ୍ଷଣ ସ୍ତରର ସ୍ତରର ପରୀକ୍ଷଣ ପାଇଁ ଯାଞ୍ଚ କରି ସଠିକ୍ ତେଲ ସଞ୍ଚରଣକୁ ନିଶ୍ଚିତ କରେ |
- ଆବର୍ଜନା ବିଲଡିଂକୁ ରୋକିବା ପାଇଁ ନିୟମିତ ଭାବରେ ପମ୍ପ ଉପାଦାନକୁ ନିୟମିତ ସଫା କରନ୍ତୁ ଏବଂ ସର୍ବୋତ୍ତମ କାର୍ଯ୍ୟକାରିତା ରକ୍ଷଣାବେକ୍ଷଣ କରନ୍ତୁ |
- ତେଲ ପମ୍ପ ସିଷ୍ଟମକୁ ଅଧିକ କ୍ଷତି ରୋକିବା ପାଇଁ ପ୍ରେରଣା-ଆଉଟ୍ ଅଂଶଗୁଡ଼ିକୁ ତୁରନ୍ତ ବଦଳାନ୍ତୁ |
- ତେଲ ପମ୍ପ ବିଫଳତାର ଲକ୍ଷଣ |:
- ପମ୍ପରୁ ଆସୁଥିବା ଅସାଧାରଣ ଶବ୍ଦ ପାଇଁ ମନିଟର - ଯେପରିକି ଗ୍ରାଇଣ୍ଡିଂ କିମ୍ବା ଚିତ୍କାର ଶବ୍ଦ, ଯାହା ଆଭ୍ୟନ୍ତରୀଣ ବିଷୟଗୁଡ଼ିକୁ ସୂଚାଇପାରେ |
- ଭିଜିଲ୍ସ ଲିକ୍ କିମ୍ବା ପମ୍ପ ବିଧାନସଭୂତି ପାଇଁ ଡ୍ରପ୍ ଯାଞ୍ଚ କରନ୍ତୁ ଯାହା ସିଷ୍ଟମରେ ଏକ ସମ୍ଭାବ୍ୟ ତ୍ରୁଟିପୂର୍ଣ୍ଣ ଭାବରେ ସଙ୍କେତ ଦେଇପାରେ |
- ହାଇଡ୍ରୋଲିକ୍ ଫ୍ଲୁଇଡ୍ ରଙ୍ଗ କିମ୍ବା ସ୍ଥିରତାର କ changes ଣସି ପରିବର୍ତ୍ତନକୁ ଦୃଷ୍ଟିକୋଣ କିମ୍ବା ଦୂଷିତ ଭାବରେ ଅନ୍ତର୍ନିହିତ ସମସ୍ୟାରେ ଅନ୍ତର୍ନିହିତ ସମସ୍ୟାକୁ ଦୃଷ୍ଟିରେ ରଖି |
ପ୍ୟାଲେଟ୍ ଜ୍ୟାକ୍ ଉପାଦାନଗୁଡ଼ିକର ଅଖଣ୍ଡତା ଏବଂ କାର୍ଯ୍ୟଦକ୍ଷତାକୁ ବଞ୍ଚାଇବା ପାଇଁ ନିୟମିତ ରକ୍ଷଣାବେକ୍ଷଣ ଜରୁରୀ | ସୁପାରିଶ କରାଯାଇଥିବା ରକ୍ଷଣାବେକ୍ଷଣ ଅଭ୍ୟାସକୁ ସୁପାରିଶ କରି ତୁରନ୍ତ ତେଲ ପମ୍ପ ସିଷ୍ଟମ୍ ସହିତ ଯେକ clased ଣସି ଚିହ୍ନିତ ସମସ୍ୟାଗୁଡିକ ସମାଧାନ କରି ଅପରେଟରଗୁଡିକ ସୁଗମ କାର୍ଯ୍ୟଗୁଡ଼ିକୁ ସୁଗମ କରିଥାଏ ଏବଂ ସେମାନଙ୍କ ଯନ୍ତ୍ରପାତି ଲିଫ୍ଟପାନ୍ ବିସ୍ତାର କରିପାରିବ | ମନେରଖନ୍ତୁ ଯେ ସକ୍ରିୟ ଯତ୍ନ କେବଳ ନିରାପତ୍ତା ବ ens ାଏ ନାହିଁ ବରଂ ସହ୍ୟ ପରିବେଶରେ କାର୍ଯ୍ୟକ୍ଷମ ଦକ୍ଷତା ପାଇଁ ମଧ୍ୟ ଯୋଗଦାନ କରିଥାଏ |
ନିଶ୍ଚିତ କରିବା ପାଇଁ ନିୟମିତ ରକ୍ଷଣାବେକ୍ଷଣ ଗୁରୁତ୍ୱପୂର୍ଣ୍ଣ |ସର୍ବୋତ୍କୃଷ୍ଟ କାର୍ଯ୍ୟଦକ୍ଷତା ଏବଂ ଦୀର୍ଘାୟୁତା |ପ୍ୟାଲେଟ୍ ଜ୍ୟାକ୍ ର | ଏକ ନିୟମିତ ସେବା ଏବଂ ରକ୍ଷଣାବେକ୍ଷଣ ଯୋଜନା କାର୍ଯ୍ୟକାରୀ କରିବା |ଅପରେସନ୍ ଡାଉନଟାଇମରୀର ବିପଦକୁ ହ୍ରାସ କରେ |ଏବଂ ଉଦ୍ଘନ ପ୍ରଦର୍ଶନ ନିଶ୍ଚିତ କରେ ଯେ ଏହାର ସର୍ବୋତ୍ତମରେ | ନିୟମିତ |ପ୍ରତିଷେଧକ ରକ୍ଷଣାବେକ୍ଷଣ |ଏଥିରେ ସାହାଯ୍ୟ କରେ |ଅପ୍ରତ୍ୟାଶିତ ବ୍ରେକଡାଉନ୍ ରୋକିବା |ଏବଂ ଦୀର୍ଘ ସମୟ ମଧ୍ୟରେ ସମୟ ଏବଂ ଅର୍ଥ ସଞ୍ଚୟ କରିବା | ରୁଟିନ୍ ରକ୍ଷଣାବେକ୍ଷଣ ଯାଞ୍ଚ କରି ବ୍ୟବସାୟ ଏବଂ ଠିକଣା ଚିହ୍ନଟ କରିପାରିବ |ସେମାନେ ବୃଦ୍ଧି ପାଇବା ପୂର୍ବରୁ ଛୋଟ ସମସ୍ୟା |ପ୍ରମୁଖ ସମସ୍ୟାରେ, ମହଙ୍ଗା ମରାମତି କିମ୍ବା ପ୍ରତିସ୍ଥାପନର ବିପଦକୁ ହ୍ରାସ କରିବା | ମନେରଖ, ସକ୍ରିୟ ଯତ୍ନ କେବଳ ସୁରକ୍ଷା ବ ens ାଏ କିନ୍ତୁ ଗୋଦାମ ପରିବେଶରେ କାର୍ଯ୍ୟକ୍ଷମ ଦକ୍ଷତା ପାଇଁ ମଧ୍ୟ ଯୋଗଦାନ କରିଥାଏ |
ପୋଷ୍ଟ ସମୟ: ଜୁନ୍ -5-2024 |